Measures to Ensure the Quality of Bulk Materials
Importance of Sampling in Goods Receipt
The use of grain is more diverse today than ever before. Various industrial sectors utilize this raw material. It doesn't matter whether the grain is produced domestically or imported.
In 2018, the largest grain-producing nations were China, the USA, and India. Germany ranked 16th with a share of around 1.3%. In Germany, over 700 different grain varieties are approved.
The main processing industrial sectors are:
- Food and beverages
- Animal feed
- Industrial use
To achieve a high quality of the final product, it is of fundamental importance that the raw materials used are of high quality and purity. There can be numerous reasons that make further processing of the raw material impossible. These include pathogens, impurities, infestation, contamination, as well as the use of pesticides or genetic modifications.
Processing low-quality raw materials can have financial or health consequences. Additionally, costs and loss of reputation arise from recalling the material. For this reason, checking the raw materials at the beginning of the processing processes is of essential importance.

The REMBE® truck sampler
Sampling from the Truck at Goods Receipt in Mills and Mixed Feed Plants
In mills and mixed feed plants, most raw materials are delivered by truck. Sampling at goods receipt fundamentally differs from sampling within the processing processes. While inline samplers such as cup, screw, or piston samplers are used there, manual samplers are often still used for taking sample material from the truck.
Manual sampling has various disadvantages. Manual extraction is very time-consuming and, of course, includes the "human" factor. This means that the sampling depends on the knowledge and daily condition of the person entrusted with the extraction. Often, the sampling is carried out by the truck drivers themselves. The result is that the sampling is not always representative and reproducible, which, however, must be a core element of qualitative sampling. Additionally, the safety of the employee taking the samples must be ensured at all times. This means that appropriate climbing aids must be available on-site so that sampling can be carried out safely.
Probenahme nach DIN-Norm
Many companies also place importance on the sample being taken from the truck in accordance with DIN standards. The standard "DIN EN ISO 24333" "sets requirements for the [...] sampling of cereals and cereal products [...] for the purpose of assessing quality and condition." The standard describes how reproducible sampling should be carried out. In addition, the ratio between the total quantity and sample quantity, as well as the individual sampling points in the truck, are defined in order to obtain a representative average sample. For a total quantity between 15 and 30 tons in the truck, the standard requires 8 sampling points to be approached in a specific pattern, and depending on the application, between 1-10 kg of sample material to be taken. Figure 1 shows the pattern to be approached for 8 sampling points.
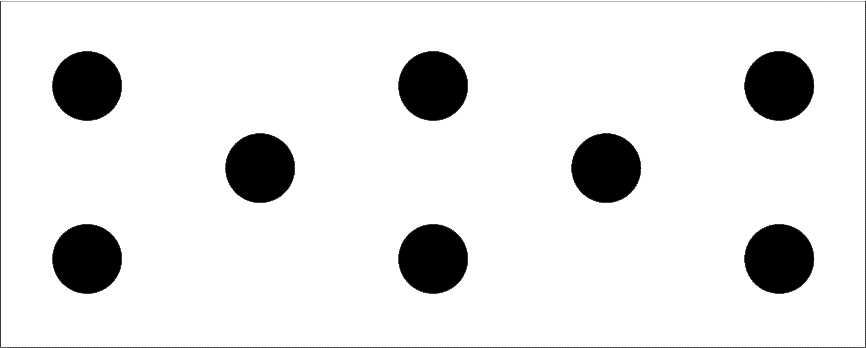
Figure 1: Sampling points for trucks with 15-30 t material according to DIN EN ISO 24333.
Der LKW-Probenehmer von REMBE® Kersting
To enable sampling according to the requirements of the standard, while also leveraging the advantages of automatic sampling, REMBE Kersting GmbH has developed a portal sampler. Depending on the design, this can be mounted on 2 or 4 supports.
The goal is to offer companies the opportunity to take the required sample quantities at the required positions in the truck fully automatically. To do this, a lance is driven into the material, and the sample is suctioned out.
The sampling can proceed in the following steps:
Positioning of the truck under the sampler.
Opening of the tarp on the top of the truck by the driver.
Release of the truck for sampling by pressing a button.
Automatic approach to the defined points depending on vehicle size and geometry.
Extraction of material.
The advantages of the REMBE® truck sampler
The advantages of the REMBE® truck sampler lie primarily in the speed of sample collection. The automated approach to the sampling points eliminates the tedious and time-consuming positioning of the sampling lance at the right spot in the truck. For sampling according to the pattern from Figure 1, the truck sampler requires only 6 minutes from the start release to the receipt of the sample.
Because the control of the lance is computer-driven and the influence of the employee is reduced, a representative and reproducible sampling is always ensured.
The extracted sample can then be filled into bags using the Sample Butler, another product from REMBE® Kersting, which are directly sealed and labeled with production-related data such as supplier, batch number, and date/time. Another option is the direct sample transport to the laboratory via hoses or pipelines.
We are happy to assist you in implementing your sampling concept. An existing sampling system can be viewed by arrangement.