Sample transportation in industrial quality assurance using the example of granulation
Consistent process monitoring is the cornerstone of modern quality assurance. Only through regular monitoring can it be ensured that the produced material meets the requirements. It doesn't matter whether it's a process in the food industry, medicine, or chemistry.
The core element of process monitoring is the control loop consisting of the steps
- "Recording of process parameters",
- "Analysis of parameters",
- "Deriving adjustment requirements", and
- "Implementation of changes",
similar to the PDCA cycle or Deming cycle. Increasingly rapid production processes to boost production also require more closely timed monitoring. As a result, the time between sampling and receiving measurement data in, for instance, the food industry, which previously took hours, must continually be shortened.
![[Translate to English:] [Translate to English:]](/fileadmin/REMBE_Kersting/Produkte/RKG_Probentransportsystem_B600.png)
[Translate to English:]
Granulate
Granulation generally refers to the process by which one or more powders are transformed into a grainy form, known as granules. This can be achieved either through pressure or with a binder. There are various reasons for granulation, such as:
- Avoidance of material separation due to different particle sizes
- Improved flowability due to the reduced adhesion of the granulate compared to the powder
- The granulate has a lower static charge potential than the powder
- Larger particles reduce dust contamination
Like any other process, granulation must also be monitored. Suitable for this are samplers that take a sample in the most product-friendly manner, e.g., cup samplers.
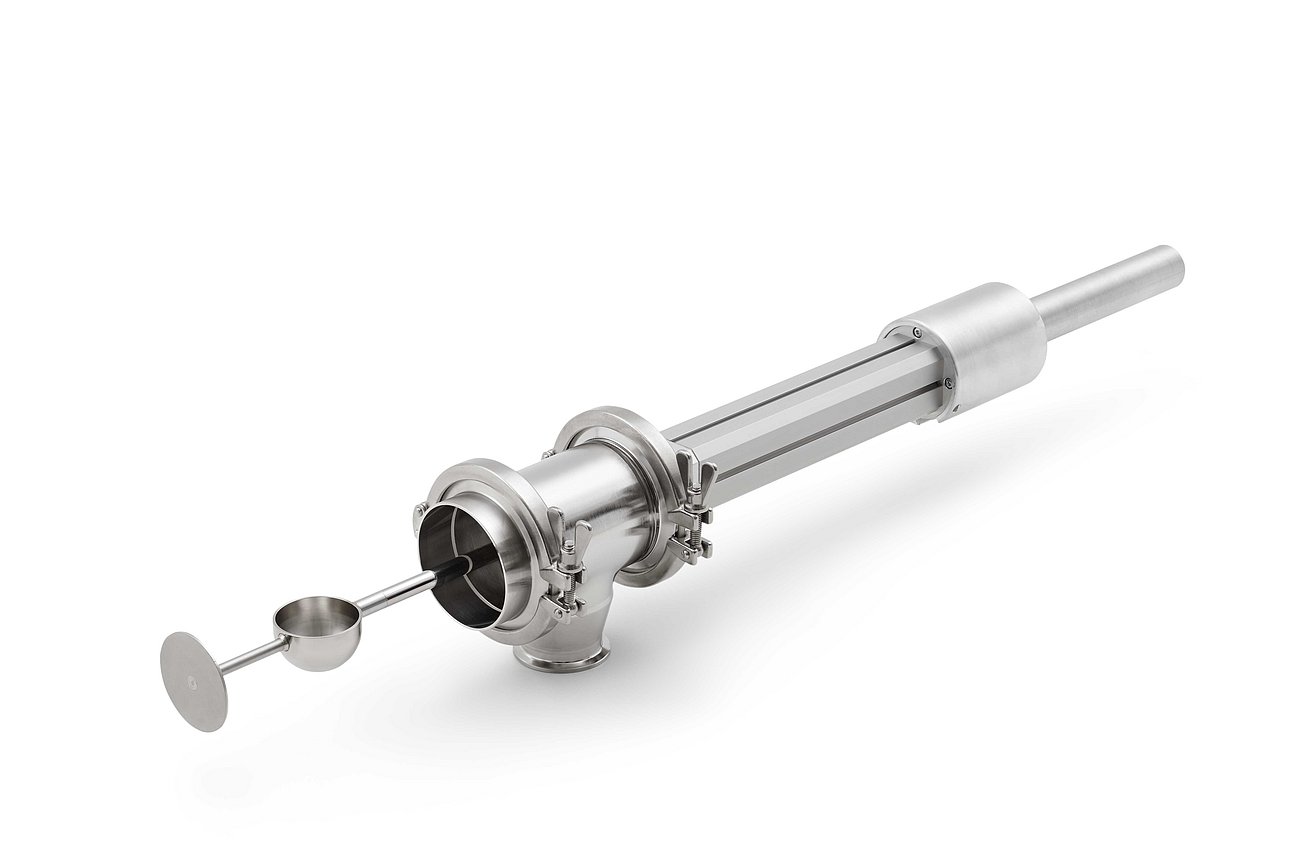
FIG1: REMBE® Kersting SAMGlide
These samplers are used in processes where maximum product protection is paramount. Since the material is collected in a sample cup, there is no impairment of the material, for instance, if it were taken with a screw. After sampling, the step of sample analysis follows, for example, using a particle analyzer or a near-infrared spectrometer, to detect possible deviations from the target state and thus derive possible adjustment requirements.
In this context, it is relevant where in the process the sampling and analysis take place. The four concepts of "Inline", "Online", "Atline", and "Offline" are distinguished. The graphic below illustrates these relationships.
Pneumatic Sample Transport
Since the end of 2022, the company "SIMAR® GmbH" has been a firm part of the REMBE® Alliance. This has added a very important partner to the group, which already includes companies like "REMBE® Safety + Control GmbH" and "REMBE Kersting GmbH". A core business of SIMAR® is the pneumatic transport of bulk materials. Many points need to be considered to ensure the quality of the sampled materials is not influenced and to obtain an unadulterated analysis result:
- Product protection: the material's properties must not be affected during transport. For example, grain grinding and material separation must be minimized.
- Stability: the pipes and hoses used should not wear out, especially with abrasive materials.
- Foreign material: It must be ensured that no foreign materials are introduced.
- Cleaning: The transport device must be easy to clean dry to prevent drag and thus cross-contamination, especially when processing substances with high requirements, such as FDA, containment, or toxicity.
- Small quantities: Systems must be able to reliably transfer even small amounts of a few grams.
Simar Conveyor Device
For these and similar applications, Simar® has developed a conveyor device. It's a compact conveyor device specifically for small systems. The conveyor device is made of stainless steel, making it easy to clean and maintain. Since it is delivered ready for operation, it can be easily integrated into existing systems. The microprocessor control allows integration into the system's control system. The conveyor device is suitable for grain sizes from 0.5 - 5 mm. With a low height of only 590 mm and a consumption of only 1.0 kW, it is a good alternative to large conveyor systems, making it ideal for retrofitting in connection with the installation of sampling.
Speed Increase and Cost Savings through Sample Transport
Due to the ever-accelerating production processes, constant process monitoring is important today to ensure that all requirements are met. This means that the time between sample collection and analysis must be shorter. REMBE® Kersting aims to make a contribution with its samplers and the corresponding conveyor devices to carry out the collection and analysis of the samples as inline as possible, meaning on-site. This is the only way to respond consistently and promptly if the material parameters deviate from the desired state. In the end, it's a matter of the costs that arise when material has to be discarded due to errors.
Author: Jonathan Blum, Dipl.-Wirt.-Ing. (Global Sales)