C-LEVER® in Food Processing for Detecting Exact Flow
In the bulk material industry, the throughput of material is of fundamental importance to the process. This is also the case in the food sector. This constantly presents companies with the same challenge: how do I detect the exact flow? Whether during goods receipt, storage, truck loading, or within a production process. At all these interfaces, it is important to capture accurate values. The C-LEVER® is a REMBE® Kersting flow meter for mass measurement of free-flowing bulk materials. Flour, grain, sugar – the C-LEVER® can be integrated into these and many other processes.
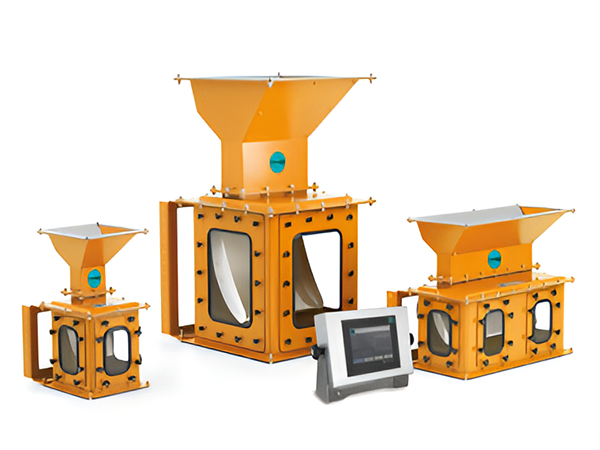
C-LEVER® and EVA HighEnd
Dosing and Performance Monitoring
The C-LEVER® is frequently used in food processing for dosing and performance monitoring. For the production of high-quality foods, it is essential that the individual ingredients are processed in the correct ratio. Incorrect mixing ratios mean that produced batches cannot be reused. For this reason, an easy-to-integrate flow meter is needed, which allows measuring ingredient quantities automatically in flow. The C-LEVER® can be easily integrated into existing processes. Flexible adaptation solutions allow the system to be connected to different pipelines or systems. Material can be fed via various systems, such as rotary valves, screws, or sliders.
Most production plants in the food industry are now controlled via a central control system in which all process data and machine parameters are collected and monitored. The C-LEVER® fits seamlessly into this. The EVA HighEnd transmitter allows the mass flow to be read at any time. The measurement signal can also be integrated into the control system via analog and digital interfaces. Remote configuration via the Internet offers a convenient way to set up the system. In addition to using the C-LEVER® as a pure measuring system, it can also be actively used for process control.
The transmitter has various relays. With them, switching signals can be output, which offers the possibility to control plant systems depending on the flow measurement. This allows automatic dosing according to a predefined recipe. For example, the transmitter can give an automatic switching signal that stops material conveyance once a certain flow quantity is reached. Even with fluctuating material flow, the same amount is processed consistently since the actual material quantity is measured. This ensures high process quality.
Truck Pre-loading
Another important area of application for the C-LEVER® is truck pre-loading. In many companies, loading is still done the old way. This means that the truck drives over a scale before loading to determine its empty weight. The loading then takes place – often without the use of a measuring system – solely based on feeling and experience. After loading, the truck continues to the customer.
Only occasionally is there a control weighing, which reveals that too much or too little material has been loaded. Both are problematic. Overloading can result in fines for the driver and the plant operator. Even with too little loading, there are financial losses, as a full batch is always invoiced. Every trip to the scale and any subsequent loading or unloading of the vehicle is time-consuming and incurs additional costs. This problem is effectively circumvented by using the C-LEVER®. The C-LEVER® is installed at the material outlet.
The truck driver can see how much material the vehicle is being loaded with during the loading process. By storing the material parameters in the transmitter, this value is automatically displayed to him. The employee can end the loading when the target value is reached. The aforementioned relays of the transmitter also allow automatic control of the loading systems. When the stored quantity is reached, the loading is automatically stopped. Manual termination by an employee is not necessary.
Inventory Control
Inventory monitoring is of fundamental importance in every production. This is also the case in food processing. Only if it is always known how much raw material is available can processes run smoothly. Information errors can lead to production downtime. This ultimately results in production downtime, which incurs costs. To avoid this risk, the C-LEVER® is connected to the storage silo or storage container. This way, every material withdrawal can be recorded. Once a defined minimum stock level is reached, the electronics emit a signal. Based on this, new material can be reordered and the warehouse restocked. This effectively prevents production downtime.
For food processing, this type of mass measurement is a major advantage. The C-LEVER® offers reproducible measurement with the highest accuracy and a wide variance of flow quantity. This makes it suitable for use in various areas of the food industry. Process parameters such as temperature, density, and explosion risk do not stand in the way of precise mass measurement. There is a suitable model for all applications. In addition, the C-LEVER® does not use any moving parts. This guarantees that it is a wear-resistant and low-maintenance flow meter, and also prevents the loss of batches due to detached components or materials. The robust C-LEVER® is therefore suitable for a wide range of applications in the food industry.
REMBE® Kersting GmbH kompetenter Partner
Customers worldwide know the bulk material experts of REMBE® Kersting GmbH as competent partners for measurement technology solutions and automation of representative sampling. The established company creates sustainable benefits through:
- Flow measurement technology for powders and bulk materials
- Silo weighing for new installations and retrofitting to existing plants
- System solutions for optimizing the supply chain
- Professional sampling for seamless quality control
Optimizing processes and workflows is one of the most important tasks that REMBE® Kersting devotes its full attention to. The bulk material experts develop, manufacture, and deliver products that make customers' production processes safer and more profitable.