Sampling from mixers with wall-mounted agitators.
Whether pharmaceutical products, food/feed, or minerals, reliable quality assurance today requires companies to constantly monitor to meet prevailing quality standards and guarantee seamless traceability. Customers have high expectations and demand compliance with the standards and quality characteristics. Due to increasingly complex processes, one must ensure that the supplied substances match the specifications. Depending on the product or process, hazards to humans and the environment may otherwise arise.
Processing low-quality raw materials can also have financial implications. Additionally, there are costs and reputation losses due to material recalls. For this reason, the verification of raw materials at the beginning of the processing process is of paramount importance. Samplers are used for reliable quality assurance in the following areas:
- Upon goods receipt to check the delivered quality,
- In production for precise process control, and
- During filling and loading for output control.
Selection of the Right Sampler
In general, the specific use case must be thoroughly examined before using a sampler. The following factors influence the choice of the sampler:
Material Parameters: Important for the sampler's choice is whether the process material is solid, liquid, or gaseous. Additional parameters such as viscosity or chemical properties must also be considered.
Process Parameters: In which area is the sampler used? Each environment imposes its own requirements on the sampler's material and the seals used.
Flow Speed: How fast does the process material flow? The sampler must be designed for the forces exerted by the material.
Pressure: Higher pressures in the system pose greater challenges to the sampler than systems operating at ambient pressure. Negative pressures should also be taken into account.
Temperature: The materials used in the sampler must be able to withstand the process and material temperatures.
ATEX: If the sampler is used in an explosion-prone environment, it must be designed for this purpose. Installation Location: The planned installation location has a significant influence on the sampler's choice. Here, the primary distinction is between stationary (e.g., in tanks, silos) or flowing (e.g., in pipelines) materials. For instance, a cup sampler can only be used in applications with falling material. In contrast, auger samplers can also be used in containers filled with material.
Collision Consideration: If movable parts are located within the process space, such as in mixers, care must be taken to avoid collisions with the sampler, as these often lead to damage and plant failure.
The next section, therefore, focuses on the peculiarities of sampling in mixers.
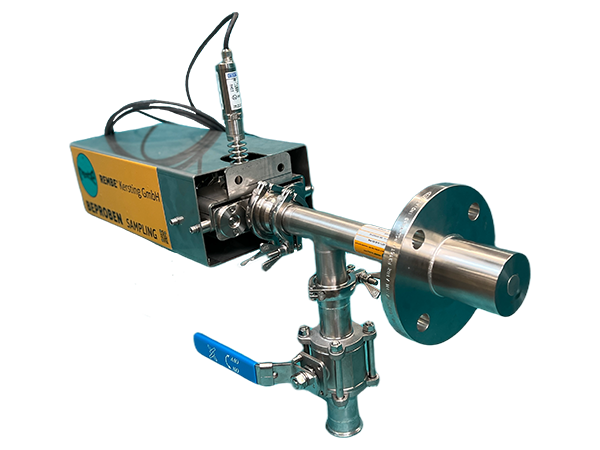
SAMscrewtasty
Challenges in Sampling from Mixers
Mixers come in various designs and applications. However, when the agitator is flush-mounted, there is a risk of colliding with the sampler during operation. There are various ways to prevent a collision:
- Install the sampler only when the agitator is not installed, e.g., with fold-out agitating mechanisms, or when it's stationary. As a result, no samples can be taken during the mixing process.
- Design a recess in the agitator for the sampler. This allows the sampler to remain continuously in the process without colliding. On the other hand, this can lead to dead spaces or insufficient mixing of the material.
- Design the sampler so that it is flush with the container wall and can still take material. For this purpose, REMBE® Kersting GmbH has developed a new pneumatic sampler, which will be discussed in the next section.
Mobile Auger Sampler
The following illustration shows the structure of the new pneumatic "SAMscrewtasty", specially developed for mixers with flush-mounted agitators. The sampler is equipped with an auger that can also move linearly. The sampler can be separated from the environment with the red hand lever.
The sampling is done in 6 steps:
- The sampler is in its basic position. The auger has moved all the way forward, pressing against a sealing surface in the welding flange.
- The auger moves back pneumatically, opening a sample chamber.
- The agitator introduces process material into the sample chamber.
- The auger rotates forward, closing the sample chamber.
- The sample is carried to the sample outlet by rotating the auger backward.
- The sampler is back in its basic position, ready for another sampling. This design ensures that no material enters the auger in its basic position. Additionally, the process is sealed from the environment, making the system suitable for hygienic applications.
This design ensures that no material enters the auger in its basic position. Additionally, the process is sealed from the environment, making the system suitable for hygienic applications.
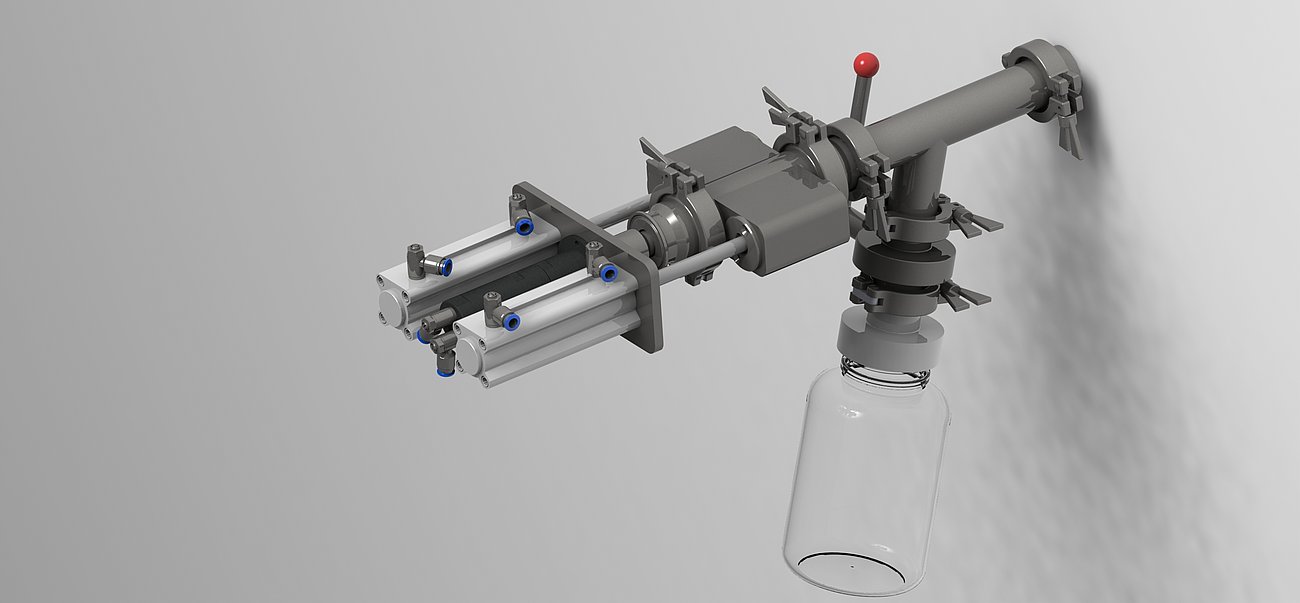
The sampling is done in 6 steps
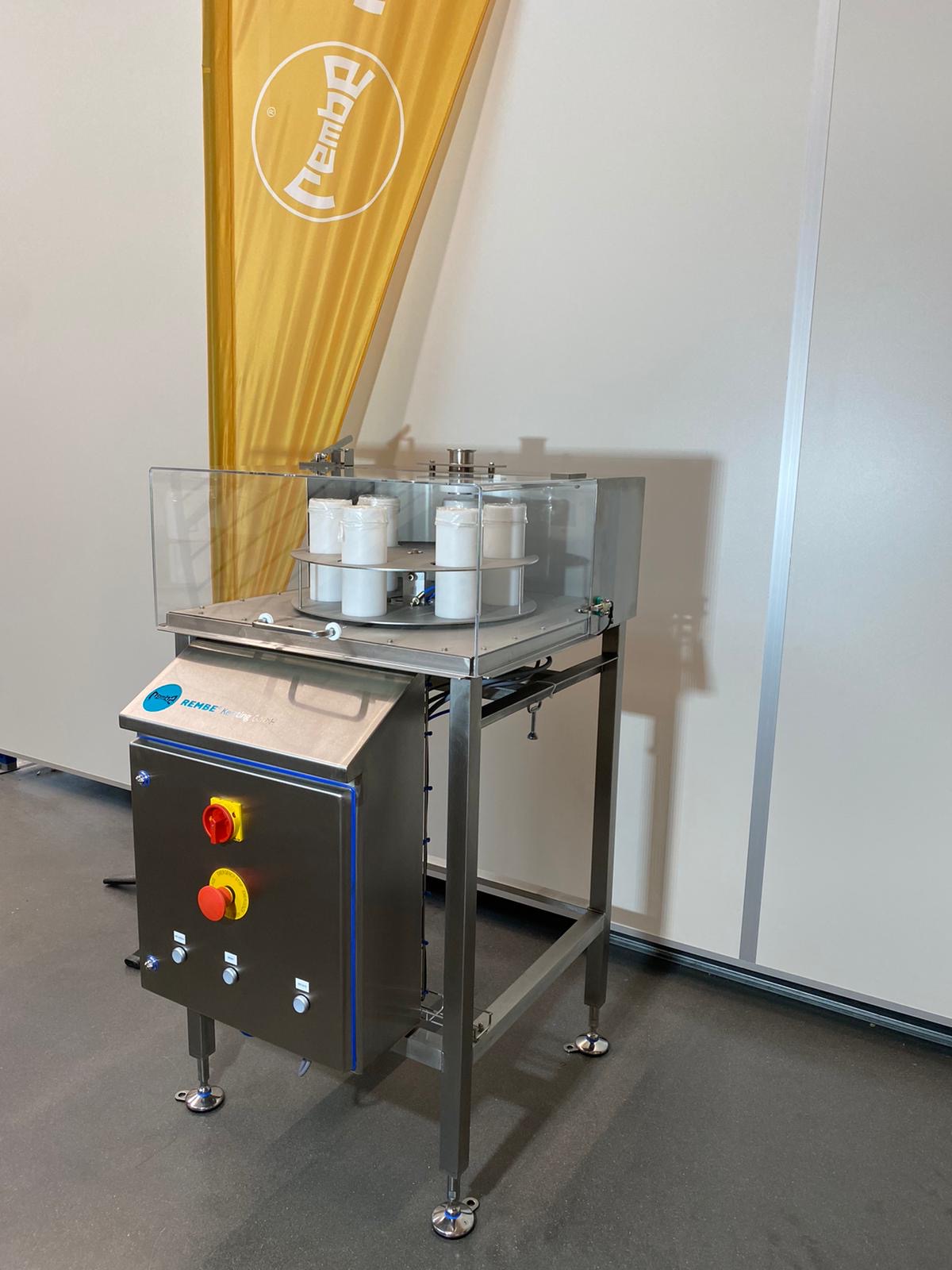
Sample carousel
Collection and Processing of Samples in Sample Carousel and SAMbutler
Apart from the traditional form of collecting samples in individual sample containers mounted below the sampler, the sample carousel can be used as a system for sample collection. These are sample bottles positioned on a turntable. For each sampling, the plate rotates one position further. This enables multiple sample containers to be filled automatically without having to change the individual containers manually in between. If necessary, this can also be done under a protective atmosphere. In addition to the sample carousel, REMBE® Kersting's sample butler can be used for fully automatic filling, sealing, and labeling of samples and retention samples.
Additional benefits are provided by integrating analysis systems for automatically collecting material parameters, such as grain sizes, moisture, bulk density, or protein content, and the complete integration of the sample butler into the existing IT infrastructure.
The subsequent illustration shows the sample butler in use after a mixer to package, label, and provide multiple samples from the batch fully automatically for further processing after each mixing. The sample butler is approximately 2,000 mm high, 1,200 mm wide, and 700 mm deep. If the packaging and analysis systems cannot be placed near the samplers, pneumatic sample transport can be used.
We would be happy to assist you in implementing your sampling concept on-site.
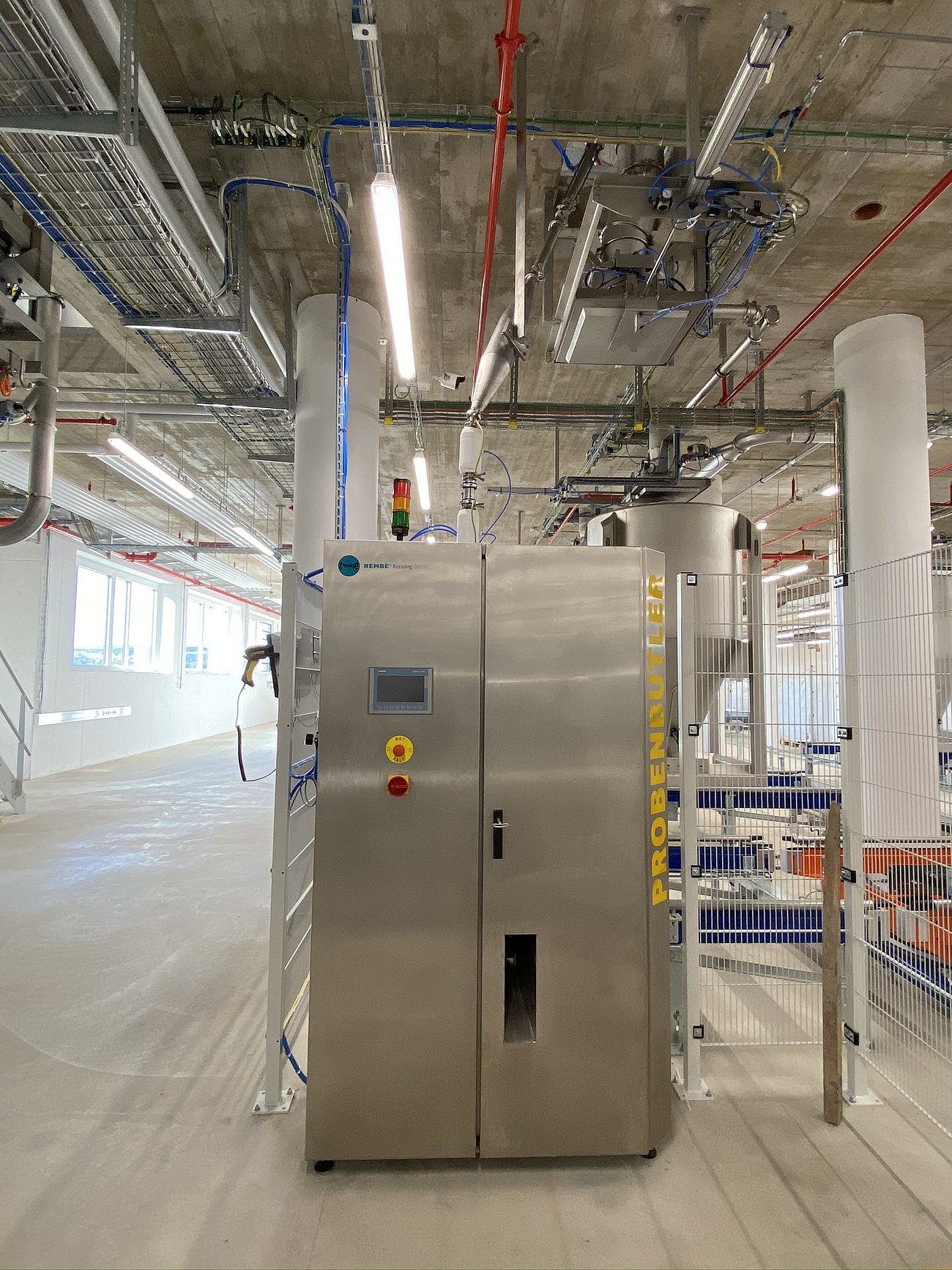
SAMbutler in use